The World’s First Fully
Recyclable Printed Circuit Board Substrate.
Jiva has developed a fully recyclable and biodegradable PCB substrate – Soluboard®.
Now with PTH compatibility!
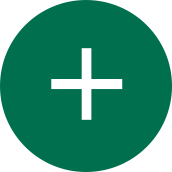
The Problem.
It is common for PCB manufacture to form the largest share of an overall carbon footprint for an assembled product.
For example, it is believed that 68% of the carbon created during the manufacture of laptops is generated when producing the assembled PCB.
62 million tonnes of Waste Electrical and Electronic Equipment (WEEE) was produced in 2022, with 82 million tonnnes expected to be produced in 2030.
PCBs make up 42% of e-waste by weight, making them the highest contributing polluter to WEEE.
Mainstream PCB laminates are constructed from glass-fibre and epoxy. The only commercial method of processing incumbent PCBs involves shredding and incinerating them to extract the precious metals within.
This inefficient process is very energy intensive, costly and polluting, resulting in a substantial loss of value of any precious metals recovered.
6 million tonnes of carbon emissions are produced annually from existing PCB disposal and recycling processes.
It is estimated that close to £8 billion of high-value precious metals and critical minerals is sent to landfill every year, releasing high levels of heavy metals, toxins and dioxins into the natural environment.
High numbers of electronic waste are exported to developing countries. It is estimated that only 17% of European e-waste is properly tracked for collection and recycling.
The Solution.
The patent protected Soluboard® is an alternative rigid PCB laminate with improved environmental credentials that is compatible with two-layer PTH designs.
Soluboard® is manufactured by impregnating natural fibres with a water-soluble polymer and a halogen-free flame retardant. The composite material is then consolidated and supplied to PCB fabricators as panels of copper clad laminate (CCL) available in a range of sizes.
Soluboard® can be taken from bare laminate through to an assembled PCB using equipment available to a standard PCB fabricator.
It is fully compatible with processes including water-based etching, electroplating, drilling, routing and curing.
It is estimated that 11.42kg of carbon per square metre of Soluboard® PCBs would be saved compared to the same area of market incumbent PCBs.
This means that Jiva’s customers can benefit from a carbon footprint reduction of up to 67% if Soluboard® is adopted at scale. Up to 590g per square metre of plastic would also be prevented from entering the waste stream at end-of-life when switching to Soluboard®.
Soluboard® PCBs have the most significant impact when integrated into the supply chain of customers offering take-back schemes for their products at end-of-life.
Soluboard® is the ideal solution for Corporate Social Responsibility (CSR) directives that have been adopted because of the consumers’ desire to better understand the environmental impacts of their products.
Proud members of
The European Institute for the PCB Community (EIPC) is an expanding international service provider to the European Interconnection and Packaging Industry. The EIPC has serviced 120 member companies since 1968, including machinery suppliers, materials and software tools to the PCB industry, along with PCB manufacturers and OEMs. Business owners, senior management and technical staff find the EIPC is an efficient platform for following new developments in the industry.
The Institute of Circuit Technology (ICT) was established in 1974. Since then, it has successfully provided technology-based training and seminars to the UK’s PCB technologists and engineers, keeping them up to speed with developments in the industry. The ICT facilitates improvement in standards by providing opportunities for its membership to improve their knowledge of manufacturing process technologies, materials, and practices through research, discussion and seminars around the country.
Composites UK is the Trade Association of the UK Composites Industry. Their aim is to promote the UK composites industry in every conceivable manner so that it may continue to grow and to compete in the ever more competitive world of global composites production. Their mission statement is ‘to promote the use of composite materials to the widest market spectrum’.